Welding sapphire wins over Bourdon company
Bourdon needed a technology capable of transparent laser welding. Laser Cheval provided the solution with a 3-axis Saphir machine. It is fast and precise. The benefits are numerous for this company, which specialises in high-precision mechanical pressure measurement technology.
Transparent laser welding
Bourdon, a subsidiary of the Baumer group based in Vendôme (41), is a world leader in mechanical process instrumentation. The industrial company has earned this international recognition by developing specific know-how in mechanical pressure measurement technology with a high degree of precision. It was with the same exacting standards that Laser Cheval responded to the detailed needs of the customer's specifications. "We therefore designed and installed a machine capable of performing laser welds by transparency on membranes with a thickness of 25µ to 0.1 mm and a diameter of 15 to 100 mm on pressure separators."
Saphir 3 axes, fast and precise
The Saphir 3-axis is a dedicated laser welding machine that incorporates fibre optic technology with a scanner head driven by software that we developed in-house, guaranteeing a simpler, more intuitive human-machine interface. The Saphir Lew's tilt galvanometric head can be rotated from -10°/+90°, making it ideal for welding around the workpiece.
This technology streamlines production
This technology is a real plus in the organisation of Bourdon's production, as it enables the company to work on several product ranges. In addition to pressure separators, we weld bellows for pressure switches and thermostats, diaphragms for capsule pressure gauges, and sensitive elements for pressure transmitters. The materials are also different, with the Saphir handling stainless steel/stainless steel and stainless steel/hastelloy/monel/stainless steel. Our customer has gained in flexibility with this laser, which replaces digitally controlled YAG technology in its workshops.
Finer welds
In terms of the final result, the weld is finer, enabling more regular production on thin materials (25µ) with a smooth, aesthetic bead. Finally, the good repeatability has helped to improve the scrap rate by more than 80%, and the cleanliness of the welds is consistent with the requirements of hygiene standards.
Optimum repeatability
There has been a real improvement in production with optimum repeatability, particularly for thin materials. Time is also saved and penetration is controlled. In the end, Bourdon notes that this technology has enabled it to rationalise production by transferring 10% of the products in its range from TIG welding to a laser welding positioner. This means reduced energy consumption and space savings.
For further information
contact us on 03 81 48 34 60 or by e-mail laser@lasercheval.fr
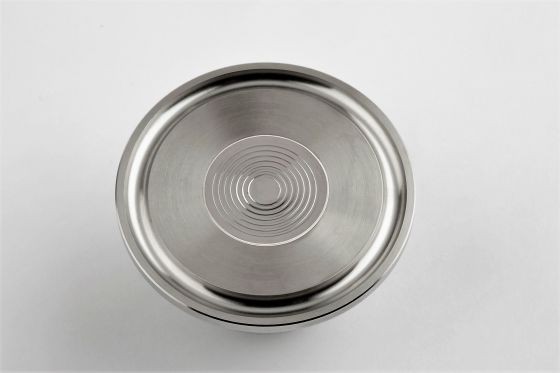